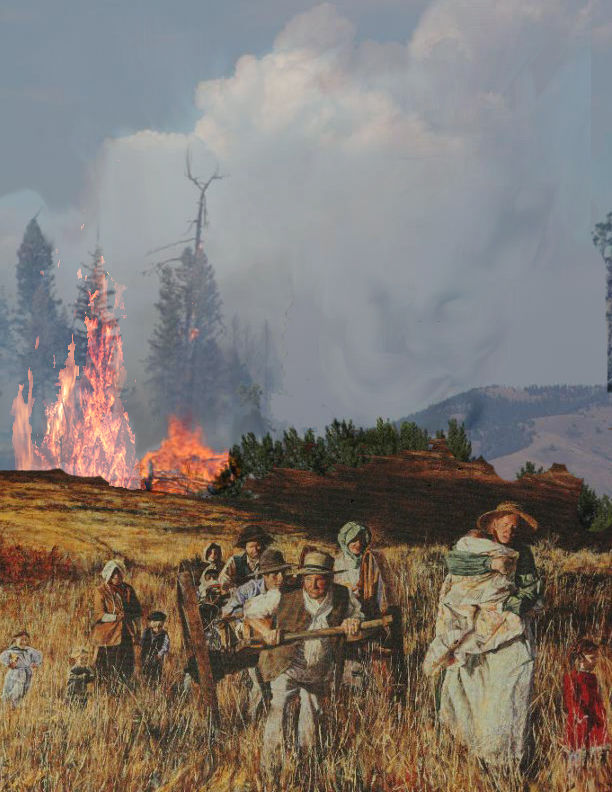

PHYSICAL STRUCTURE OF TARGETED MOLECULES IN NATURAL GAS AND DECOMPOSITION GAS.
Alternative to the Claus Process
UpStream Desulfurization
G. Allan Oram
​
ABSTRACT
​
The questions of how to cost-effectively remove inefficient compounds from, and whether or
not it is feasible to charge a battery, or fuel cell with decomposition gasses is not new. Opening
the closed system will inhibit normal entropy faced in current battery technology [[i]]. It is
feasible to build and experiment with a novel open-system battery, or fuel cell that will recharge
itself through the input of decomposition gases [ii]. As an added effect this novel approach
could lead to a cost-effective refining means for removal of H2S and CO2 from mid and smallscale
decomposition gas resources, and result in an energy rich resource that will require no
combustion of fuels [[ii]].
​
HYPOTHESIS
​
The energy resources being discussed are diagrammed in the molecular model (photo) above.
The target molecule CH4, is mixed together with a number of other different compounds that
are present in natural, or released during the decomposition process in decomposition, gas.
These resources are most notably witnessed by the heated smoke column in a forest fire, but
they are also found at municipal wastewater facilities, landfills, Dairy Farms, etc. Every molecule
in natural, or decomposition gas other than CH4 limit the efficient use of natural gas. To
become a viable energy producer for human societies, the CH4 moieties must be eluted away
from all the other gases in a refining process.
​
Refining refers to the time-dependent removal of unwanted elements in a mixture. Current
research is focused on separating the valued hydrocarbons from the unwanted thiol and ketone
contaminants in energy rich gases. The intended purpose is to increase the energy content for
cost-effective conversion processes, and eventual end-use by human populations. Refining
assumes major importance in the petroleum and natural gas industries. Due to the high
importance of both water and petroleum in human activities [[iii]] refining technologies have
received a major amount of attention in recent years.
​
The technology exists to operate at cost-effective refining efficiencies on large scale application,
but current technology is incapable of replicating cost-efficiencies for overall refining processes
on mid and small-scale application. (I.E. mid-small scales are considered a refining capacity that
is not capable of processing 100-million cubic yards of unrefined natural gas per day.) In this
section focus will be placed on the mechanisms that cause mid and small-scale refining
application failures. The intended outcome is to test feasibility of novel decomposition gas
refining technologies that will not require combustion, at mid to small scales.
​
HISTORY
​
Natural gas is formed during the decomposition of organic matter [[iv]]. Over millennia the
earth sequestered this gas in underground reservoirs. The highly valued substance in natural
gas is CH4, but it contains other substances, such as: N2, He, Hg, H2S, CO2, among others [ii].
Because natural gas is a result of decomposing organic matter, contemporary technology can
capture and sequester these gasses at the point of the decomposing organic matter. Thus, these
unwanted gasses are trapped before decomposition vents more greenhouse gas to the already
taxed atmosphere. For economic purposes, the methane and other energy content therein must
then be separated from the impurities, and converted into pertinent energy sources designed
specifically for human use, and revenue generation.
​
Like ethanol in gasoline, impurities in natural, or decomposition gasses generally corrode and
deteriorate pipeline, and other metal storage components, destroy combustion engine
components, and inhibit the energy content in end use systems. These impurities must be
removed or “scrubbed” before the gas can become an economic source of energy [[v],[vi]].
Once CH4 is eluted away from the impurities, the impurities, some toxic, and most a form of
environmental pollution must as well be utilized. Absorption technology through a solution of
alkanolamines or Benfield are the most common contemporary processes used world-wide to
“scrub” natural gas of CO2 and H2S content [iv]. Once these compounds are sequestered, the
CO2 is typically vented, and the toxic H2S undergoes a sulfur reclamation process invented by
Carl Friedrich Claus [[vii]]. However, the Claus process is considered too expensive, and too
complex for mid and small scale natural, or decomposition gas refining processes [[viii]].
Therefore, utilization of most decomposition gas resources as a means for energy to power
conversion is inefficient with current technology [[ix]]. If competitive technology for
purification of methane content in decomposition gasses were available for mid, or small-scale
application, the world's forests, human dumps, wastewater facilities, and a great number of
dairy farmers, for instance, could offset greenhouse gas emissions, and operational costs by
providing electrical power, or other energy forms to the grid [vii].
​
Technically anything that decomposes overtime would then become a valuable source of energy
for human uses. Though trees would need to undergo a pyrolysis process, the show-stopper is
not at that point. The current showstopper, is the Clause Process, and its inability to "cost
effectively" remove hydrogen sulfide, H2S, gasses from a cloud of gasses smaller than a million
cubic yard. If the "Fire for Resource Benefit" process were implemented on large scale a great
many natural energy resources would then become viable, and cost competitive with the current
natural gas industry. These sources are clearly the trees burning every year in a wild fire, but
they also include city wastwater facilities, landfills, and the most notable resource for energy at
this time, Dairy Farms.
​
It is estimated that 125,000 dairy cows produce 80 million pounds of methane annually. This is
equivalent to roughly 315 thousand tons of carbon dioxide emissions [[x]]. These emissions are
becoming a concern, as it is estimated that animal agriculture emits 18 % of total anthropogenic
emissions world-wide [[xi]]. It is also estimated that utilization of anaerobic digesters could
sequester all 80 million pounds of bovine produced methane, both reducing anthropogenic
emissions, while providing energy to the growing energy network [x]. However, there are issues
involved, most political, with mid and small-scale decomposition gas refining processes that
make it cost-inefficient.
​
Identifying social, technical, and other variants in decomposition gas digestion, and innovation
to determine the path of future development in the field of science [[xii]], there are many
different forms of refining in contemporary society:
1) Polyethylene Glycol Scrubbing,
2) Chemical Absorption,
3) Pressure Swing Adsorption,
4) Bio-filtering,
5) Cryogenic Separation, and
6) Membrane separation.
​
Each refining process faces its own set of variables and obstacles. Generally, energy conversion
using Dairy Refuse feedstock increases environmental acidification and eutrophication [[xiii]].
Notably, the acidification has posed a most difficult conundrum. Eutrophication is essentially
diverted through large lagoons. In these lagoons, the high nitrogen effluents into rivers and
streams are typically averted. This aversion is apprized at a cost of venting greenhouse gasses;
emissions containing energy components that are currently wasted.
​
Development of new refining technology to capture the gasses that are currently wasted, could
improve the energy content in decomposition gas, and produce a byproduct that may become
an efficient substitute for natural gas [[xiv]]. These prospected technologies would also
contribute to a considerable anthropogenic decrease in greenhouse emissions, and
eutrophication to rivers and streams world-wide.
​
PRIOR "DAIRY" RESEARCH
​
Washington State University has conducted chemical absorption testing. The absorbents used
for the analyses were mono, and diethanolamine. Conclusions found that a 10 %
monoethanolamine solution removed 100% of the carbon dioxide in just 1 minute. However,
after the amine solution reached saturation, no further CO2 removal occurred until the
solution was regenerated. This regeneration process is lengthy, complex, and costly, and is the
part of the Claus Process that typically makes the current system cost-ineffective. The reaction
is exothermic. Hypothetical conclusions provide that large-scale removal of H2S processes are
available, but no H2S removal processes were analyzed in the study [viii].
​
Western Washington University analyzed the cost feasibility of “scrubbing” with solutions of
sodium hydroxide, and diethanolamine. Conclusions show that sodium hydroxide is not a
viable method of refining decomposition gas. A continuous need for input of sodium
hydroxide showed its initial inefficiency. Along with the continual input, the hydrogen sulfide
transport and storage facilities deteriorated rapidly and required routine replacement [viii].
Using diethanolamine [[xv]] as the absorbent a Western Washington University study
successfully eluted CH4 away from the impurities in Dairy Farm created decomposition,
greenhouse gasses, and converted it to a near pure form of biogas [viii]. However, the system
provided several operational challenges that are currently being addressed, pilot-scale, at
VanDeRHaak Dairy in Lynden, WA. These inefficient results are shown through the continual
existence of decreased pressures as the gasses elute through the system. Pressure drops that are
a result of leaks, caused by structural failures of metallic components, joints, and valve
apparatus [viii]. Though not emphatically stated in the study, the cause of the structural
degradation can be ascertained as a result of higher than norma fugacity of CO2 and H2S in the
system.
​
All of the existing biogas to energy conversion methods are intended to provide fuel for
combustion processes. Even with the multimillion dollar initiative, the current technology is
not cost effective for mid and small scale application [viii].
​
PROCESSES
​
At this point in human evolution it is theoretically inept to burn anything, if there is a process
available in which decomposition gas energy conversion to electrical power does not involve
combustion. "Fire for Resource Benefit" then becomes twofold: “sweetening” the biogas
(removing contaminants) and, “sweeting” and conversion of the available energies in a single
step through voltaic pile, or fuel cell technology [ii].
​
The most sought after component of any gas, for energy conversion purposes, is elemental
hydrogen. The laminar flame speed of pure hydrogen is 1.47 m/s faster than diesel fuel, and
1.43 m/s faster than gasoline fuel [[xvi],[xvii]]. It is 0.0145 m/s faster than methane [[xviii]].
The increased vapor pressures make hydrogen the energy sources sought. All hydrocarbons are
laden with energy potentials due to their hydrogen content. One other compound in the
mixture of decomposition gasses contains hydrogen. The thiol compound of H2S. However,
when combusting H2S, it requires the mixture of oxygen. Once the exothermic reaction occurs,
it produces sulfur dioxide, mixed with steam and given the proper catalyst (heat of formation) it
forms sulfuric acid.
​
H2S(g) + O2(g) --> SO2(g) + H2O(g)
​
2 SO2(g) + O2(g) + catalyst --> 2 SO3(g)
​
SO3(g) + H2O(l) --> H2SO4(l)
​
This acid corrodes metallic components, and provides a myriad of inefficiencies in systems
transport, and storage facilities of current technologies. Hulls Dairy, in Corvallis, Montana, has
the anaerobic capacity to digest bovine excrement, in much the same manner as
VanDeRHaack’s Dairy in Lynden, WA. The problem, as is the problem in all of the other 260
dairies nationwide that also have digester capacities [[xix]], H2S and CO2 moieties in resulting
decomposition gasses corrode and destroy combustion engines, and storage, and transport
components at an exponential rate [[xx]]. The result is constant replacement of damaged
components. Replacement expenses prove the systems to be cost-ineffective [[xxi]].
As explained earlier, refining technology in the petroleum industry is designed for large scale
application. This technology, mainly the desulfurization, or sulfur reclamation "Claus"
processes is not efficient for the mid and small scale applications that are required in these
dairy’s [viii]. Thus, the installment of retrofitted technology is needed to provide efficient
decomposition gas to energy conversion.
​
HAZARDS
​
H2S is a toxic gas, found in the Sulfide, and Inorganic reactive groups [[xxii], xx]. When put
into contact with O2 and powered Cu, or O2 and BrF5, OF2, ClF2, AgCNO, it explodes [[xxiii],
xx]. When put into contact with HgO, CaO, Tl2O3, Na2O2, AgO, AgO2, MnO2, NiO, CuO,
PbO2, BaO2, CrO3, HNO3, PbO2, Pb(ClO)2, AgBrO3, Cu2Cr2O5 and rust, it ignites [[xxiv],
xx]. It may ignite in rusty pipes [[xxv], xx]. The exothermic reaction produced when combined
with Ba(OH)2, KOH, NaOH, soda lime, and oxygen may cause ignition or explosion [xx].
Therefore, extreme caution and safety protocols must be adhered at all times when working
with, or around the substance.
​
METHODS
​
H2S has an energy component, two atoms of hydrogen. It is inefficient to waste this
component. There are myriad technologies that utilize thiol compounds. The most notable
energy conversion processes are chemical reactions in a voltaic cell. It is also noted that electric
current was the defining affect to help scientists originally isolate a number of elements [iii].
Essentially, some of the energy extracted from a lead acid battery is Gibbs energy. These “free
energies” are a result of the strong acid’s disassociation with a proton [[xxvi]].
​
H2SO4(l) --> H+(l) + HSO4-(l)
​
This reaction occurs before the acid is inserted into the voltaic cell. Because the cell is divided in
half, the anode half and the cathode half. In a lead-acid battery, when in discharge while the
anode oxidizes, reduction occurs at the cathode [[xxvii]].
​
(-)Pb(s) + HSO4-(aq) --> PbS04(s) + H+(aq) + 2e-
​
(+)PbO2(s) + 3H+ + HSO4-(aq) + 2e-(s) --> PbSO4(precipitate) + 2 H2O
​
When recharging both the anode and cathode switch polarities, while the arrows in the
identifying equation reverse directions. In essence an “ion-pump” drives the chemical reactions
at the “electrode-electrolyte interfaces” while using the electrolyte (HSO4) for internal resistance
[[xxviii]]. There are a number of possible solutions to avert the toxic effects, and volatile nature
of H2S. Because it may explode and ignite when put into contact with lead, or lead oxide, it
appears to be the show stopper to filtering for energy conversion through a lead acid battery.
Nevertheless, the technology exists [ii]. The technology also exists to strip sulfuric acid of
Hydrogen. This is the mechanism that provides electricity from a storage battery. Further
research and study for possible implication and eventual decomposition gas to energy
conversion without the use of combustion as a means for energy conversion through a voltaic
pile, or fuel cell is warranted.
​
Novel Ni anode (8 % NiO doped with Y and stabilized by ZrO2) inhibits coking (deterioration)
effect of independent catalyst layers within metal oxide fuel cells that operate on methane based
fuels. Providing a stabilized environment for voltage throughput, novel fuel cell voltage
degradation went from 0.6 V in 20 minutes, in non-doped fuel cell, to 0.03 V in 12 hours in
doped cell [[xxix]]. The interpretation of structural solid oxide fuel cell degradation due to realtime
conditions are structurally sound, and available for the lead acid version.
​
Another method involves upstream catalytic fractionation of biogas that provides high
hydrogen content syngas, and biomaterials form carbon nano-fibers in the electrolyte which can
be processesed into synthetic graphite [[xxx]]. In both methods, high methane fugacity shortens
redux time [[xxxi]], while producing high amounts of carbon deposits in dry reforming
cathode/anode recovery of hydrogen. It is also relevant to the proposed project that the biogases
used in the former and latter study, injected in the pile or fuel cell, were already “sweetened”.
Refining of H2S compounds in decomposition gas can theoretically be completed inside a
voltaic pile of sorts in a single step [ii]. If this proves inefficient, a Mobius
strip has brought this proposal back to the initial problem. Upstream catalytic fractionation of
H2S must occur in a cost-friendly manner, before mid or small-scale refining operations will
become cost-efficient.
​
Acidithiobacillia, or Thiobacillus oxidize sulfur [[xxxii]]. These bacteria convert hydrogen
sulfide into sulfuric acid [[xxxiii]]. This sulfuric acid can then be utilized as electrolyte for
battery technologies. The materials already exist to house sulfuric acid in lead acid batteries,
therefore, it could prove to be a viable means to remove H2S from decomposition gasses [ii],
and the proposed open system will improve battery technologies [i]. While H2S is toxic to
metalloproteinase, other substances are found to bind with H2S, for instance, the iron sites in
hemeproteins specifically found in sea clams [[xxxiv]], or in extracellular hemoglobin at the Cys
+ 1, and Cys + 11 of deep sea annelids [[xxxv]]. Battery and refining technologies could discover
a considerable technological advancement through the proposed novel refining processes.
This is an energy to power conversion that does not involve the combustion of fuels. If the
battery proves inefficient, once the CH4 is sufficiently “sweetened” it can be processed through a
combustion to energy process' nevertheless "Fire for Resource Benefit" is founded upon the basic
principle that in this day and age it is inept to burn anything.
​
The main purpose of "Fire for Resource Benefit" is to investigate feasible processes needed for
separation of decomposition gas components, to maximize efficiencies in energy output for
non-combustion conversion of energy content. To do this, it may not necessarily entail the
construction of a model biorefinery, as the electrochemical reaction inside the fuel cell, or
voltaic pile may provide the answer.
​
REFERENCES
​
[i] Layton, B. E., Noell, S. L., Oram, G.A. Entrophy acceleration, Shannon information and
socioeconomics: quantitative examples. International Journal of Design & Nature and
Ecodynamics. 2016. Vol. 11, No. 1. Pp. 48-63.
​
[ii] Pujare, N. U., Tsai, K, J., Sammells, A. F. An electrochemical Claus Process for sulfur
recovery. Journal of the Electrochemical Society. 1989. Vol. 136, iss. 12, pp. 3662-3678. DOI:
10.1149/1.2096528
​
[iii] Cracolice, M.S., Peters, E.I. General chemistry: an inquiry approach. Cengage learning.
2012. pp. 5.1, 6.4.
​
[iv] Shimekit, B., Mukhtar, H. Natural Gas Purification Technologies – Major Advances for
CO2 separation and future directions. Department of Chemical Engineering, University of
Teknologi PETRONAS, Malaysia. Web accessed at: http://cdn.intechopen.com/pdfs/35293/
InTechNatural_gas_purification_technologies_major
_advances_for_co2_separation_and_future_directions.pdf
​
[v] Tobin, J., Shambaugh, P., Mastrangelo, E. Natural gas processing; the crucial link
between natural gas production and its transportation the market. Energy Information
Administration, Office of oil and gas. 2006. Web accessed at: https://www.eia.gov/pub/oil_gas/
natural_gas/feature _articles/2006/ngprocess/ ngprocess.pdf
​
[vi] NaturalGas.org. (2010). Overview of Natural Gas, In: Background, 22.06.11, Web.
Accessed at: http://naturalgas.org/overview/background/
​
[vii] Lagas, J.A., Borsboom, J., & Berben, P.H. (1988). Selective-oxidation catalyst improves
Claus process. Oil Gas J.;(United States), 86:41.
​
[viii] Zhao, Q., Leonhardg, E., MacConnell, C., Frear, C., Chen, S. Purification technologies
for biogas generated by anaerobic digestion. Center for sustaining agriculture and natural
resources. Research Report, 2010. Web accessed at: http://www.build-a-biogasplant.
com/PDF/BiogasPurificationTech2010.PDF
​
[ix] Hui, G., Heng, X., Jian, E. Z., Kaijkun, W., Hainan, G. The development and application
of biogas refining technology. Renewable Energy Resources, 2013. Vol. 31 no. 5. Pp. 103-108
ref. 25
​
[x] Sjoding, D., Lyons, K., Kruger, C. Recycling Energy. Case Study: Vander Haak Dairy,
Lynden, W.A. Northwest CHP Application Center. Combined heat and power for the states of
Alaska, Idaho, Montana, Oregon and Washington in cooperation with the U.S. Department of
Energy. December 2005. WSU EDP05-025. Web accessed at:
http://www.northwestchptap.org/NwChpDocs/VanderHaakDairyCaseStudy.pdf
​
[xi] Liu, Z., Powers, W., Oldick, B., Davidson, J., Meyer, D. Gas Emissions form Dairy Cows
fed typical diets of Midwest, South, and west regions of the United States. Journal of
Environmental Quality. Vol. 41. Technical Reports. Atmospheric pollutants and trace gasses.
Nov. 17, 2011. DOI: 10.2134/jeq2011.0435
​
[xii] Markard, J., Stadelmann, M., Truffer, B. Prospective analysis of technological
innovation systems: Identifying technological and organizational development options for
biogas in Switzerland. Research Policy, Volume 38, Issue 4, May 2009, Pages 655–667. http://
dx.doi.org/10.1016/j.respol.2009.01.013
​
[xiii] Bühle, L., Hensgen, H. Donnison, I., Heinsoo, K., Wachendorf, M. Life cycle assessment
of the integrated generation of solid fuel and biogas from biomass (IFBB) in comparison to
different energy recovery, animal-based and non-refining management systems. Bioresource
Technology Volume 111, May 2012, Pages 230–239. http://dx.doi.org/10.1016/
j.biortech.2012.02.072
​
[xiv] Hui, G., Heng, X., Jian, E. Z., Kaijkun, W., Hainan, G. The development and application
of biogas refining technology. Renewable Energy Resources, 2013. Vol. 31 no. 5. Pp. 103-108
ref. 25
​
[xv] Huang, K., Zhang, XM., Hu, X.B., Wu, Y.T. Hydrophobic protic ionic liquids tethered
with tertiary amine group for highly efficient and selective absorption of H2S from CO2. AIChe
Journal, vol. 62, iss. 12. Pp. 4480-4490. DOI: 10.1002/aic.15363
​
[xvi] Korsakova, A. I., Gubernov, V.V., Bykov, V., Maas, U. 2016. The effect of soret diffusion
of stability of rich premixed hydrogen-air flames. International journal of hydrogen energy.
Vol. 41, issue: 39, pp. 17670-17675. http://dx.doi.org/10.1016/j.ijhydene.2016.07.141.
​
[xvii] Ortenzi, F., Giovanni, P., Ramadhas,. A.S. 2011. Alternative Fuels for Transportation.
Ed. Ramadhas. S. Hydrogen. pp. 243-293. CRC Press. 2011. Boca Ration, Fl.
ISBN:978-1-4398-1957-9.
​
[xviii] Ranzi, E., Frassoldati, A., Grana, R., Cuoci, A., Faravelli, T., Kelly, A.P., Law, C.K.
Hierarchical and comparative kinetic modeling of laminar flame speeds of hydrocarbon and
oxygenated fuels. Elsevier. 2012. Progress in Energy and Combustion Science. Vol. 38, pp.
468-501.
​
[xix] EPA. Livestock anaerobic digester database. PageLink. AgSTAR Database of Livestock
Digesters. June 15, 2016. Web accessed at: https://www.epa.gov/agstar/livestock-anaerobicdigester-
database [xx] Personal observation, 2013-2016.
​
[xxi] Personal Communication, Dan Hull, owner operator, Hulls Dairy, October 2016. [xxii]
Cameo Chemicals, Reactive Group Datasheet. Office of Response and Restoration, National
Ocean Service, National Oceanic and Atmospheric Administration, USA.gov. Web. Accessed at:
https://cameochemicals.noaa.gov/chemical/3625
​
[xxiii] Mertz, V. et al., Ber., 1880, 13, p. 722
[xxiv] Mellor, 1947, vol. 10, p. 129, 141
​
[xxv] Mee, A. J., School Sci. Rev., 1940, 22(85), p. 95
​
[xxvi] Denker, J. Lead-Acid Battery : principles of operation. 2004. Web. Accessed at:
https://www.av8n.com/physics/lead-acid.htm[xxvii] AUS-e-TUTE. Lead-Acid Batteries
Chemistry Tutorial, 3 January 2017. Web. Accessed at:http://www.ausetute.com.au/
pbbattery.html
​
[xxviii] Saslow, W.M., Voltaic cells for physicists: two surface pumps and an internal resistance.
Am. J. Phys. 67 (7), July 1999. Web. Accessed at:
http://www.elp.uji.es/masterNNM/docencia/refs/1999%20AmJPhys%20Saslow.pdf
​
[xxix] Chang, H., Chen, H., Shao, Z., Shi, J., Bai, J., Li, S.D., In situ fabrication of (Sr, La)FeO4
with CoFe alloy nanoparticles as an independent catalyst layer for direct methane-based solid
oxide fuel cells with a nickel cermet anode. Jounral of Materials Chemistry A. 2016. 4,
13997-14007. DOI: 10.1039/C6TA04639H
​
[xxviii] De Llobet, S., et al. Catalytic decomposition of biogas to produce hydrogen rich fels for
SI engines and valuable nanocarbons. International Journal of Hydrogen Energy. 2013. Vol. 38,
issue, 35. PP. 15084-15091. Doi: 10.1016/j.ijhydene.2013.09.086
​
[xxviii]M. Herrer., Plou, J., Durna, P., Herguido, J., Pena, J.A. Hydrogen from synthetic biogas
via SIP using Nial2o4 catalyst: reduction stage. International Journal of Hydrogen Energy. 2015.
Vol 40, issue, 15. Pp. 5244-5250. DOI: 10.1016/j.ijhydene.2015.01.063
​
[xxix] Kelly, D.P.; Wood, A.P. (2000). "Reclassification of some species of Thiobacillus to the
newly designated genera Acidithiobacillus gen. nov., Halothiobacillus gen. nov. and
Thermithiobacillus gen. nov.". Int. J. Syst. Evol. Microbiol. 50 (2): 511–6.
doi:10.1099/00207713-50-2-511
​
[xxx] [xxxiii] Selman A. Waksman; J.S. Joffe (1922). "Microorganisms Concerned in the
Oxidation of Sulfur in the Soil II. Thiobacillus Thiooxidans, a New Sulfur-oxidizing Organism
Isolated from the Soil". J Bacteriol. 7 (2): 239-256
​
[xxxi] [xxxiv] Baubeta, F.M., Bari, S.E., Estrin, D.A., Boechi, L. Access and binding of H2S to
hemeprotiens; the case of HBL of Lucina pectinate. J. Phys Chem B. 2016. 120(36): 9642-53.
DOI: 10.1021/acs.jpcb.6b06686
[xxxii] [xxxv] Baily, X,. Riwanon, L., Carney, S., Colin, O., Xal, F., Toulmond, A., Jollivet, D.
The loss of the hemoglobin H2S-binding function in annelids from sulfide-free habitats reveals
molecular adaptation driven by Darwinian positive selection. PNAS, May 13, 2003. Vol. 100, no.
10, pp. 5885-5890. Web. Accessed at: http://www.pnas.org/content/100/10/5885.ful.pdf