


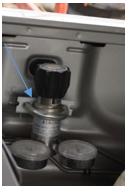
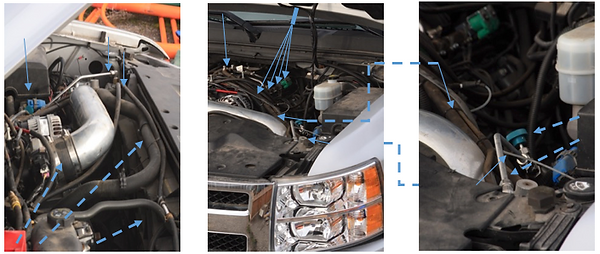

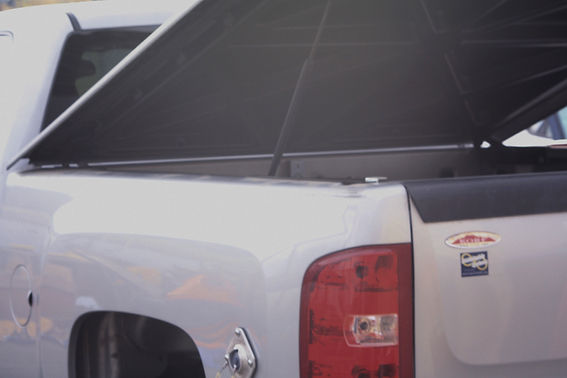



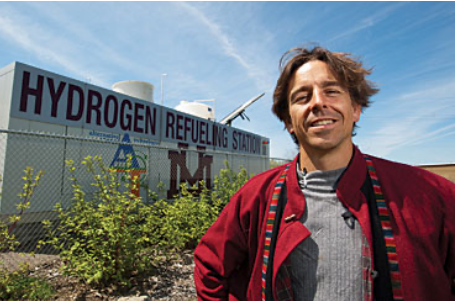
Dr. Bradley Layton standing in front of the Hydrogen Fuel Station, Missoula Montana.
The Making of Hydrogen Power
These pickup trucks are hybrid gasoline/ethanol/natural gas/hydrogen fueled vehicles. With the flip of a switch on the dash, a driver can switch the engine to operate on any one of the four different fuels.
​
GM truck type model: C10753, conformed to the applicable Federal Motor Vehicle Safety Standards December, 2009. Chevrolet released this standard alternative fueled gasoline – ethanol powered vehicle for wholesale in 2010, [1]. It came stock with a 4.8-liter V-8 Vortec engine, and a 5-year, 100,000-mile factory warranty. Its powertrain is connected to a 4-speed automatic transmission. The Silverado full‑sized pickup truck sold for $29,125. With the addition of an HD trailering package PK6, and a driver’s side adjustable seat, this particular Chevrolet Silverado, before hydrogen conversion cost $31,070. Fuel economy ranged from 11-to-12 miles per gallon (mpg) during city driving, and ranged from 15-to-30 mpg during highway travel. With a combined average of around 16 mpg [2]. Factory ratings rated this vehicle to travel between 370 and 502 miles on a full tank of gasoline. Factory ratings rated this vehicle to travel between 264 and 370 miles on a full tank of ethanol [3].
​
Upon research into the itemization of just one of these pickup trucks, after it was purchased, stock, from Hank at Korf Continental, in Sterling, Colorado it was retrofitted with a turbo-charger and combined natural gas pack, then refit to operate on hydrogen. Along with the pickup trucks, a hydrogen refueling station was built along I-90, in Missoula, Montana.
​
The pickup trucks and hydrogen fueling station were part of a hydrogen initiative [5] in Montana's, Missoula Valley, during the late 2000’s. To replenish onboard storage hydrogen fuels, a hydrogen balloon station electrolyzer and compression pump were retrofitted. Their purpose was to act as an interstate hydrogen depot refueling station along I-90, and to keep the retrofit Chevy Silverado's fueled for the future.
​
BACKGROUND – H2 ISSUES, SAFETY AND STORAGE
​
Efficiency, maximum power, and greenhouse gas emissions are “multi-objective” issues hydrogen-powered internal combustion spark engines face, [6]. In connection with these up‑front problems, hydrogen powered SI (spark ignition) engines also experience backfire issues through the course of normal operation, [7]. Backfire in hydrogen engines occurs predominantly due to a 6-percent burning rate—increase—in the laminar flame speed of hydrogen, which is 1.47 m/s faster than diesel fuel, and 1.43 m/s faster than gasoline fuel, [8],[9]. This presents safety issues when hydrogen is used as an alternative fuel in transportation vehicles.
Other safety issues with hydrogen-fueled transportation vehicles are associated with onboard storage of the gaseous fuel. Hydrogen’s volatile nature and dissociative properties when it comes in contact with oxygen present additional challenges, as does hydrogen’s low density: at ambient pressure one kilogram of hydrogen occupies a volume of ~11 meters cubed, [10],[9]. With a power conversion ratio of 2.3-to-1, compared to gasoline, onboard storage of hydrogen for transportation vehicles requires twice the volume capacity as that of gasoline to achieve the same driving distance, [10], [9]. Given the physical characteristics, it is prudent to compress hydrogen into onboard storage fuel tanks. This gives hydrogen twice the driving distance as compared to a gasoline powered vehicle. However, compressing hydrogen adds extra safety concerns when it is used as an alternative transportation fuel. One issue is that compressing the gas increases the overall enthalpy of the system, and could contribute to pre-ignition-combustion and backfire.
Onboard hydrogen storage is usually composed of either a high-strength steel, an austenitic type steel, or an aluminum cylinder, incased in a stabilizing dielectric such as fiberglass, [10]. Pressures in these cylinders can sometimes reach 550 bar, [9]. Though hydrogen is a non-toxic gas, special care must be taken to avoid rupture of pressurized storage tanks and hydrogen manifold feeder lines. Due to high pressures, if tanks rupture, or the feeder systems malfunction, a static charge could pose an ignition source, or coupled with other ignition sources, hydrogen jets can create detonation shock waves comparable to many atmospheres, [9] as was experienced in one of the most tragic hydrogen disasters of all time—The Hindenburg, [10]. Another danger with hydrogen gas is asphyxiation.
Asphyxiation is a safety concern when working with hydrogen in enclosed spaces. In order to avert most hazards associated with the storage and normal engine operation of hydrogen‑powered SI engines, certain safety protocols must be adhered to when working with or around hydrogen-fueled transportation vehicles. These safety concerns create issues when malfunctions occur in duel-fuel systems, such as gasoline systems converted to operate on hydrogen.
Licensed automotive dealers will not repair minor malfunctions in gasoline components of duel-fuel gas/hydrogen systems, because of insurance issues and internal company policy. The other and larger issue is that even though hydrogen increases engine performance, the chance of hydrogen leaks in enclosed garages that do not contain the proper hydrogen gas detectors is a very critical safety concern.
H2 POWER AND FUEL DELIVERY
​
The application of hydrogen as an alternative fuel in spark combustion engines increases SI engine performance and advances start-up capacity, as compared to gasoline-fueled engines, [12]. When compared to gasoline engines, hydrogen-fueled engines decrease hydrocarbon and oxygenated carbon emissions by 58.3-percent and 40-percent, respectively, [13]. As hydrogen is a carbon free fuel source, all the carbonized emissions created by a hydrogen powered vehicle are assessed in the manufacturing stages, and not the operational stages. Hydrocarbon powered vehicles and electricity are used to create the beasts. If on the other hand, hydrogen fuel were used to manufacture automobiles, and create electricity these vehicles would register at net-zero for carbonized greenhouse gas emissions.
When applying hydrogen as an alternative fuel for SI engines, thermal NOX emissions may increase, [6], [13] because of the laminar flame speed of hydrogen. It is not fuel specific. It is a matter of thermodynamics. It requires elevated temperatures, 1800 Kelven and beyond, to break N2 triple bonds, [14]. Air containing nitrogen inside the combustion chamber experiences a rapid, almost instantaneous increase in enthalpy. This intense thermodynamic environment is known as one Zel’dovich mechanism for NOX formation, [15].
Installation of a turbo-charging unit as an addition to the SI engine, and or adjustment of the air-to-fuel ratio alleviates any formation of NOX emissions, [10]. It is believed that very little nitrogen dioxide (NOX) is created by a hydrogen powered engine. However, to assure a vehicle fueled with this gas is working at net zero Diesel Fuel Exhaust systems and fluids allow an avenue to sequester and convert any unwanted NOX formations so that they are not emitted into the atmosphere. Installation of a turbo-charging unit also increases SI engine performance and advances the engine’s overall power coefficient, [16], thus decreasing the formation of greenhouse gasses, and increasing engine performance.
​
In hydrogen‑fueled SI engines there is a direct relationship between engine power output, greenhouse gas (GHG) exhaust emissions, and performance. These factors are significantly affected by exhaust gas recirculation and ignition timing [6]. Recirculation and ignition timing also reduces the probability of backfire, reducing engine safety issues and combustion knock, [7], [17]. In SI engines, engine cylinders can receive the input of hydrogen fuels in three different methods: Induction through the manifold, induction through port injection, and direct injection, [9], [13], [16].
​
Induction through the manifold is achieved by means of carburetion. Though this system allows smooth engine operation, it also increases combustion issues such as knock, rapid pressure rise in cylinders, and pre-ignition. Thus carburetion increases the probability of backfire [17], [9].
​
Induction through port injection occurs straight through the manifold intake. Individual cylinder ports use electronic injector controls to regulate hydrogen-to-air mixtures. Hydrogen enters the manifold during the intake stroke decreasing the possibility of pre-ignition, thus decreasing the probability of backfire [16], [9]. Injecting air to hydrogen mixtures also increases oxygen content in the system. Higher ratios of oxygen enable complete combustion and lower operating temperatures. Thus critical temperatures (1800 K) for NOX formation are not achieved, [18] resulting in considerably lower NOX emissions as compared to carburetion, [9].
​
Direct injection occurs in the same fashion as induction; however, rather than injecting hydrogen early in the intake stroke, in direct injection hydrogen is induced into the system late in the compression stroke much like a diesel engine, [16], [9]. This results in very little GHG emissions while increasing engine performance and power. The only downside to direct injection is that injection pressures must exceed combustion cylinder compression pressures, for proper performance and efficiency, adding enthalpy to the system. Stable injection pressures range anywhere from 5 to 300 bar depending on engine capacity, [19].
Proper injector timing, and the use of exhaust gas recirculation, significantly reduce the chance of hydrogen system rupture, and/or explosive breaches that produce operational safety hazards and backfire. As with all vehicle power trains, proper handling and storage for fuel systems reduces the potential of non-operational hazards associated with flammable fuels and pressurized systems.
MAKING QUAD-FUEL-POWERED VEHICLES
​
All three of Chevy Silverado were retrofitted with onboard hydrogen-natural gas storage tanks, fuel feeder systems, and turbo charging units. Proper timing is also key to efficient operation. If these trucks were not precisely timed, they would backfire and stall out.
​
The pickup trucks were designed to start and warm up on gasoline or ethanol. When they reach operating temperature, the fuel systems are switched with a button on the dash, to operate on compressed natural gas, or with an advanced timing system hydrogen. CNG has a stoichiometry of ~17-1, seventeen mole of oxygen to one mole of CNG, while the correct stoichiometry of hydrogen is ~32-1.
​
In 2017 the gasoline stock system, or the gasoline/ethanol side on one of the vehicles malfunctioned. At first it appeared a hectic mess, because commercial automotive repair facilities would not even diagnose the issues. This left us little choice but to diagnose and fix the issues ourselves.
​
Energy Consultation and Materials Design Analysis
​
The quad-fueled pickup truck had entered “limp-mode.” Limp mode in gasoline fueled vehicles is usually triggered when one of the computerized sensing units triggers a hard code in the engine or chassis. A hard code is enacted when the engine computer detects a malfunction in one of the engine’s primary systems. It is important to note that the gasoline/ethanol computer actuated this sensor warning, this affected none of the aftermarket hydrogen and natural gas upgrades.
These sort of circumstances usually arise when a stock sensor has sensed something amiss in the engine or chassis, or when an important electronic sensor has failed on some level, [22]. Initially the quad-fuel Chevrolet was taken to Karl Tyler Chevrolet for service, a licensed automotive dealer and repair facility in Missoula. Due to aftermarket installations, the turbocharger and the natural gas-hydrogen system, and safety concerns with the onboard hydrogen storage tanks and feeder lines, Tyler Chevrolet refused to fix the malfunctioning gasoline system. Tyler officials explained insurance issues prevented the company as a whole from repairing the gasoline (stock) fuel malfunction.
It was tasked to us then to repair the vehicle. We put the truck on computer diagnostics. It was first ascertained the throttle position sensor was malfunctioning. This sensor detects the position of the throttle pedal on the floor, and matches that position, which correlates to the amount of fuel going to the intake, with the right amount of air to maintain proper stoichiometric fuel-to-air ratios.
Post install of a new throttle position sensor the engine still exhibited malfunctioning behavior. It would start and idle but would not maintain higher rpm. Upon initiation of the turbo charger, or upon revving, stepping down on the throttle the engine would sputter and die. We left the project for a time, and when we returned to it the battery on the truck was dead. This was the second battery install in a matter of months.
Even though the pickup would not start under its own power, it did have enough power to show us the hard codes the computer’s system activated. We recorded the codes, and again reset the pickup's stock computer encoding system. Because of the power drain in the battery when the vehicle remained shut down for periods of time, we suspected a parasitic power drain in one of the two onboard computer systems. Our first impulse was to get the Silverado operating again and to check its charge voltage, to assure the alternator functioned properly. Charge voltage in most transportation vehicles needs be around ~13.4 V to charge the battery to its defined 12 V operating capacity. If the alternator malfunctioned, it could cause the parasitic power drain the pickup truck was experiencing when not in regular operation. This issue is usually a malfunction of one or more of the diodes in the alternator going to ground through the rectifier bridge. If these diodes malfunctioned, any one of the four, it would allow a two-way current throughput of energy into and out of the alternator, a situation that will discharge the battery when a vehicle is not in operation.
Improper, or low-charge voltage would also cause a myriad of problems in the vehicle's internal systems. Systems would not get enough voltage while in operation and thus would not function to specifications for proper vehicle operation. The most noted effect of this is misfire. When we were able to get the vehicle started, after overnight charging with a proper battery charger, even after throttle position sensor replacement, and after we reset the engine codes, the engine would idle but would not power-up upon stepping down on the throttle mechanism. There was also a suspicious electrical noise emitting from under the bed of the truck, driver’s side. We were still uncertain if one of the diodes in the alternator caused the non-operational power drain. Nevertheless, at this point in the process we were certain the battery was charging to optimum capacity. When affixing a digital millimeter across the battery terminals, the millimeter read well in excess of 14 V, while idling. Since we knew what the hard codes were; and upon listening to the engine while idling, we could hear a clear misfire in the cylinder system, and stopped to analyze what the computer codes identified as the engine’s or chassis’ malfunction.
The computer identified four different hard codes: PO 442, PO 300, PO 420, and PO 430. (All codes were analyzed through, OBD-Codes.com, (https://www.obd-codes.com/).
PO 442, Evaporative emissions system: means a very small leak has been detected in the fuel system. Causes of this code could range from:
1. Loose gas cap
2. Small leak/hole in fuel vapor hose/tube
3. Faulty vent O-ring seal
4. Defect in vent valve
5. Defective purge valve
6. Defective leak detection pump
PO 300, multiple cylinder misfire: at this point in the process I could hear the cylinder misfire and decided to look for other system malfunctions to see if they were causing the issue.
PO 420, catalytic converter: this code is actuated when the upstream oxygen sensor and the downstream oxygen sensor are registering nearly the same reading. The upstream sensor should fluctuate. If it doesn’t, it means the catalytic converter is worn out. However, the catalytic converter is not an item that wears out. It gets plugged as the palladium captures the greenhouse gasses, etc. . . This is usually a sign that there is a malfunction in some other system.
PO 430, catalytic converter is not working properly: this code will actuate the P0 420 code. It means the catalytic converter’s oxygen recirculation capacity is below the threshold. Causes for this code range from:
1. The down-stream oxygen sensor is bad
2. An exhaust tube leakage/blockage
3. Intake air leaks
4. Faulty fuel injectors
5. Fuel injector leaks
6. Fouled spark plugs
7. Improper timing
8. Faulty powertrain control module
​
With everything observed, and with what engine codes were telling us, I believed the pickup truck had a faulty fuel pump, which would not be detectible by fuel leaking on the ground. But could be heard under the bed of the truck, behind the driver's door, and could cause a sputtering or misfire effect in the cylinders. My second hypothesis was that a leak in the gasoline fuel injectors somewhere along the fuel rail or in the headers themself were not allowing the system to pressurize, which also may not be detectable by an observable fuel leakage. It is clear to note that at that time I did not read a throttle position sensor code. As the throttle position sensor was already replaced, and the pickup truck still displayed the same malfunction.
At that time, I stepped away from the vehicle and worked more toward human safety, using National Fire Protection Association, Standard 2, to guide my actions, [24]. The hydrogen onboard storage system was shut off in the bed of the truck and it had upward of 3000psi (~3-5 kilo-grams) of hydrogen gas compressed into it. Since the truck would start on gasoline, and idle for a long duration of time, I had a mind to simply warm the truck up and then actuate the hydrogen system. This would tell me if the fuel pump in the tank were faulty and not providing enough fuel to the engine. However, I began thinking if I attempted to activate the hydrogen system, and if the injectors or fuel rails were leaking it would mean a hydrogen leak may also occur. Something very dangerous in closed environments, or near a possible static, or other ignition source. If backflash occurred I thought the two tanks in the bed of the truck could work as a pressurized bomb. Naturally this is only hog-wash! 1) The rubber hoses that complete the fuel delivery system would burst first, 2) The regulator under the hood would stop the backlash from continuing up the feeder lines and coming into contact with the hydrogen in the storage tanks, protecting the ~3-5 kilo-grams of hydrogen in the from ignition.. 3) This is the big one; in order to set off a hydrogen fusion reaction it takes a small nuclear fission reaction to start the process. This requires highly enriched Uranium, at 90% pure, and a detonation device to start releasing the neutrons that set off this sort of reaction. However, even without the nuclear trigger, if the tanks blevvied and they had an ignition source, they could still explode, like a regular petroleum gasoline tank, with TNT potential. Yet, with the failsafes installed downstream from the onboard storage it is highly unlikely an ignition source could ever reach hydrogen compressed in the tanks.
​
There are a myriad of hazards associated with the use of hydrogen fuel. The four major hazards are associated with leaks in the fuel lines or rupture of the onboard storage tanks:
1) Asphyxiation while working in small spaces.
2) Flames from a spark ignited jet leak over the headers.
3) Explosion from flare jet and flashback into the onboard storage tank.
4) Rapid decompression.
​
Using a Bacharach Leakator ® 10, combustion gas leak detector, I first put the sensor down into the fueling port of an operational mid-size Chevrolet Colorado pickup truck. The sensor showed no change in output, in other words it detected no hydrogen gas leaks. Upon a fine tune of the Leakator's sensor array however, it began showing data detecting combustion gasses. From that point I retuned the Leakator to detect hydrogen, and ran the sensor twice over the entire 2010 quad-fueled Chevrolet Silverado. The hydrogen tanks were shut off by the shutoff valve in the bed. The sensor detected no combustible gasses near or around the full sized pickup truck.
​
Assured there were no unwanted hydrogen leaks at that time, I began repairs by looking into the parasitic power drain. I removed the DR37, 145 ampere alternator. After a rigorous testing environment, the alternator showed two failure codes: 1) bridge rectifier, 2) voltage regulator. The initial assumption was correct, one of the grounding diodes in the bridge rectifier had malfunctioned. Throughput of electrical power going both ways, while the full sized pickup truck was not in operation, and the alternator was grounding battery power into the ground mechanism, draining the battery’s charge. After replacing the alternator, I began troubleshooting the fuel systems malfunction.
​
I tested for fuel leaks under the fuel rail, or over the headers between the gasoline injectors which are separate to the hydrogen induction port injection system, that had been aftermarket drilled and inserted into the header for each cylinder just above the gasoline/ethanol fuel injectors. After starting the vehicle, which would idle but would not power up once again, I once again checked for any combustible and hydrogen gas leaks over the entire chassis, frame, engine, and in the bed of the 2010 quad-fuel full sized pickup truck. With the Leakator ® 10, I did detect combustion gasses, but with a fine tune of the device I detected no hydrogen gas leaks. With no detectible hydrogen gasses present, I still kept a fully charged fire extinguisher at the ready, while I sprayed a nominal amount of Dimethyl Ether upon each gasoline/ethanol injector, starting at cylinder 1, and ending at cylinder 8.
​
Upon application of the Ether spray, there were no detectible changes in engine idling rpm. If the fuel rails were leaking, and thus sucking excessive oxygen into the system, when I sprayed the Ether over them, Ether would get sucked into the intake. This would cause the engine to rev-up.
​
After I sprayed each fuel injector and fuel rail individually with the Dimethyl Ether, once again. Once again I noticed no detectible change in engine rpm. Because there were no changes in engine speed under the Ether spray, I was able to concluded without dismantling the entire system, the 2010 Chevrolet Silverado was probably suffering from a noisy and malfunctioning fuel pump. On this make and model the stock fuel pump is located in the gasoline fuel tank of the vehicle.
​
Mysteries Surrounding the Missoula Hydrogen Initiative
​
When the Silverado in Missoula malfunctioned, I surmised that because the truck would idle and warm up on its own if the hydrogen systems’ shut-off valves were opened, then the Commutatore Switch on the dash actuated, if the Chevy actively powered up upon stepping down on the accelerator, it would solidify my belief of a faulty fuel pump. This would save me the time I'd need to dismantle the truck's hydrogen systems, and remove the gasoline (petroleum) tank just to get to it, in order to do the proper diagnostics.
​
The hydrogen tanks had ~3000 psi (~3-5 kilo-grams) of hydrogen in them, but it had been a long time since anyone tried to operate the vehicle on hydrogen. When I opened the valve in the bed of the truck, I then threaded the long-turn shut-off valve under the hood, open. (Note, this valve should have been a 90-degree quick-turn shut off valve for safety issues--Lesson's Learned.) After the hydrogen system was charged to the intake port injectors, instead of starting the vehicle's engine on gasoline, I stopped and maintained National Fire Protection Association (NFPA) Standards, particularly Standard 2. I used the Leakator ® 10 to check for hydrogen leaks. Sweeping the combustion gas sensor over the engine, it wasn’t long until I found a hydrogen leak in a T-connection of the rubber hoses over the headers. At that time I ascertained it would be a mistake to attempt to fire the truck on gasoline with a hydrogen leak over the engine. Everything was in what appeared working order. It would be a shame to lose it due to human error.
​
After I detected the first leak, I detected further leaks. The next noted leak of hydrogen was in one of the connector, regulator, boxes over the injector. A moment later the other connector box exhibited a positive for combustion gasses. (See photos above.)
Running the sensor back over the shut-off valve under the hood, hydrogen was leaking profusely from this location. I shut the valve down and discovered the leak was in the upstream connector, between the regulator and the stainless steal tubing, a jet that I could physically feel with the back of my hand.
Returning to the bed of the truck, I ran the sensor over the bed shut off, and detected a leak coming out of the connector screw-valve. Even after I shut the system completely down, I continued to get hydrogen gas readings from everywhere in the surrounding area, for several minutes.
​
CONCLUSION -- LESSONS LEARNED
​
President George Bush signed the acts that supplied funding to this project. The Obama administration drove nails into this hydrogen funding’s coffin, and the Obama Administration implicated a simultaneous nationwide solar project initiative.
​
Because of the lack of funding, The University of Montana (U-of-M) used the land the hydrogen fueling station was erected upon to built a new Missoula College Building. In order to do this, the U-of-M abandoned the electrolyzer and the compressor pump(s). We claimed the abandoned properties, saved these technologies from the car crusher at the junk yard and have kept them safely in storage. The U-of-M did reclaim one of the three quad-powered vechicles. The other two Silverado are the property of West Virginia University, two full sized Chevrolet quad-fueled Silverado that last we knew were at the National Training Consortium of Alternative Fuels in West Virginia.
​
We concluded that in the years that the truck was in operation, the rubber hosing system had rotted and cracked. We also realized that proper hydrogen leak tape was not installed around each and every connection in the hydrogen system. With the profuse hydrogen leaks we discovered, the vehicle in its condition at the time, was unsafe for operation on natural gas, let alone hydrogen fuel. With the hydrogen system in the bed of the truck shut down, ~3000 psi of hydrogen fuel had leaked into the atmosphere in only a matter of 20 or so minutes, and the tanks were discharged. The gasoline/ethanol side of the full size pickup truck appeared fully operational, sans what I believed to be a malfunctioning fuel pump, but there are other implications to look into.
​
Addressing the misfire codes, we believe this could be caused by the aftermarket system. When the vehicle was retrofit, it was designed to loop the gasoline in the feeder lines back into the gasoline tank when the hydrogen, natural gas, system became active. With what we know, take away lessons of this testing environment show us that if the aftermarket looping back system was faulty and in operation, while the gasoline system was in operation, the onboard hydrogen computer would effectively be trying to loop petrol back into the tank, while the stock gasoline computer would effectively be trying to feed gasoline to the engine. We believe this resulted in the engine getting fuel for idling speed, but not enough fuel for higher RPM. Because there is very little communication between the two computers this is one of our two main hypotheses for the cylinder misfire at the time. If it were strictly a stock vehicle, a faulty intermittently working fuel pump would cause a vehicle to misfire, but this truck is not regular, it is novel.
​
There are existential reasons for several of the computer codes the pickup truck's stock computer was registering. This system was not designed to share its functions with another system. Therefore we hypothesize that the fuel rail or injector leaks it was registering were a result of the natural and hydrogen gas injectors. To install these injectors, the team had to drill new holes in the headers and then thread them in. This would naturally result in a stock system that was not apprised of the aftermarket retrofits to register there were pressure leaks somewhere in the combustion fuel (gasoline) delivery system, because there were. The team intentionally did this in order to retrofit the engine to operate on natural gas and or hydrogen.
We were unable to ascertain if the fuel pump was at fault, or if the looping back system, as explained above was the culprit of the cylinder misfire. We recommend further testing to ascertain which problem is actually the culprit that put the quad-fueled pickup truck into limp-mode.
Further testing is also needed to ascertain the truck's hydrogen viability. Without funds, the truck will probably never operate on hydrogen again. Documentation as the key, we were excited to finally get a chance to conclude the purpose for the funding. Funding was provided to ascertain the driving distances on a full tank of hydrogen, and a full tank of natural gas in mountainous terrain, as compared to gasoline and ethanol. The truck at the time it was retrofitted was at a Technology Readiness Level (TRL) of 6.
​
Shortly after the truck was retrofitted, President Obama drove the nails into the former hydrogen initiative's coffin, and funding was revoked. We believe that because of the lack of understanding, interest and recognition surrounding George Bush's hydrogen intuitive as it applied to the above scientific inquiry, R. Paul Williamson the head of the project at Missoula College resigned, to avoid public condemnation, rather than face public back-lash. In the interim the project gathered dust. When Dr. Bradley Layton took the helm as Dean of Missoula College's Energy Technology program he took responsibility over the former initiative. However with limited resources, documentation and no funding whatsoever available, his cognitive ability to continue the scientific inquiry was severely limited. It is believed that had the Obama Administration continued funding for hydrogen studies that at least one of our three quad-powered vehicles would have been properly tested in the operational environment, moved through TRL 8, and been at TRL 9 sometime in the early 2000-teens.
​
Before technicians can ever safely test the truck in Missoula, to ascertain its travel ranges on a tank of hydrogen, the 6+ hydrogen leaks identified beside the bed shut-off regulator, and under the hood would need be addressed first. Then the gasoline fuel feeder system would need be repaired.
​
Take away lessons for this project show that it would benefit the present state of the world's net-zero goals, if this project were rebooted with subsided funding. Through this funding the vehicles would be repaired, and the time-deteriorated appliances, fixtures, and hoses replaced, in order to move into the TRL 8 stages. Further lessons learned is that we technically understood that if the two computer systems were battling against one another, it will never create a robust environment. Merging the two onboard computer systems into one overall dynamic would bolster a more conclusive outcome, which may better benefit the battle against climate change if we took our take away lesson learned, and started over with a new system that was designed to operate on one computer hierarchy.
​
As of the writing of this article, no definitive tests have been conducted, and no data has been recorded but the data herein.
BIBLIOGRAPHY
​
[1] Vechicle Identification sticker inside panel, driver’s door.
​
[2] *Chevrolet fuel economy estimates, inside owner’s manual.
​
[3] *Chevrolet fuel distance estimates, inside owner’s manual.
​
[5] Keefe-Feldman, M. 2003. Hydrogen State. Missoula Independent. http://missoulanews.bigskypress.com/missoula/hydrogen-state/Content?oid=1134757. Accessed: 16 November, 2016
​
[6] Jabbr, Al., Vaz, W.S., Khairallah, H.A., Koylu, U.O. 2016. Multi-objective optimization of operating parameters for hydrogen-fueled spark-ignition engines. International journal of hydrogen energy. Vol. 41, issue: 40, pp. 18291-18299. Oct. 2016. DOI: 10.1016/j.ihydene.2016.08.016.
​
[7] Subramanian, K.A., Salvi, B.L. 2016. A numerical simulation of analysis of backfiring phenomena in hydrogen-fueled spark ignition engine. Journal of engineering for gas turbines and power-transactions of the ASME. Vol. 138, issue: 10, article; 102811. Oct. 2016. DOI: 10.1115/1.4033182
​
[8] Korsakova, A. I., Gubernov, V.V., Bykov, V., Maas, U. 2016. The effect of soret diffusion of stability of rich premixed hydrogen-air flames. International journal of hydrogen energy. Vol. 41, issue: 39, pp. 17670-17675. http://dx.doi.org/10.1016/j.ijhydene.2016.07.141.
​
[9] Ortenzi, F., Giovanni, P., Ramadhas,. A.S. 2011. Alternative Fuels for Transportation. Ed. Ramadhas. S. Hydrogen. pp. 243-293. CRC Press. 2011. Boca Ration, Fl. ISBN:978-1-4398-1957-9.
​
[10] Schlapbach, L., Sutte., A. 2011. Hydrogen-storage materials for mobile applications. Nature 414.6861, Nov 15, 2001. Pp.353-358.
​
[12] Hou, L.J., Xu, X.L., Gui, X.N., Ji, C.W., Wang, X., Tan, J.W., Ge, Y.S. Investigation of cold-start emissions control strategy for a bi-fuel hydrogen/gasoline engine. International journal of hydrogen energy. Vol. 42, issue: 40, pp. 18273-18281. Oct, 2016. DOI: 10.1016/j.ijhydene.2016.08.038.
​
[13] Wu, H.M., Yu, X.M., Du, Y.D., Ji, X.B., Niu, R.X., Sun, Y. Gu, J.Q. 2016. Study on cold-start characteristics of dual fuel SI engine with hydrogen direct-injection. Applied Thermal Engineering. Vol. 100, pp. 829-839. May 2016. DOI: 10.1016/j.applthermaleng.2016.02.097.
​
[14] Fluent Incorporated. 2003. Thermal NOx formation. http://jullio.pe.kr/fluent6.1/help/html/ug/node624.htm/ Accessed, 16 November, 2016.
​
[15] Kosmadakis, G.M., Rakopoulos, C.D. 2014. Computational fluid dynamics investigation of alternative nitric oxide emission mechanisms in a hydrogen-fueled spark-ignition engine. International journal of hydrogen energy. Vol. 39, issue: 22, pp. 11774-11791. July 24, 2014. DOI: 10:1016/j.ijhydene.2014.05.140.
​
[16] Quing-he, L., Bai-gang, S. 2016. Effect of the Miller cycle on the performance of turbocharged hydrogen internal combustion engines. Energy conversion and management. Vol. 123. Sept. 01, 2016. Pp. 209-217. http://dx.doi.org/10.1016/j.enconman.2016.06.039.
​
[17] Luo, Q.H., Sun, B.G. 2016. Inducing factors and frequency of combustion knock in hydrogen internal combustion engines. International journal of hydrogen Energy. Vol. 41, issue:36, pp. 16296-16305
​
[18] Eichlseder, H., Wallner, R., Freymann, R., Ringler, J. 2003. The potential of hydrogen internal combustion engines in future mobility scenario. SAE 2003-01-2267.
​
[19] Verheldst, S., Wallner, T. 2009. Hydrogen-fueled internal combustion engines. Progress in Energy and Combustion Science 35:490-27.
​
[21] Energy Consultation Materials Design personal experience.
​
[23] 23 OBD-Codes.com. Your OBD-II trouble codes repair site. AAF Official Site. https://www.obd-codes.com/. Accessed 23, October 2016.
​
[24] NFPA 2: Hydrogen Technology. http://www.nfpa.org/codes-and-standards/all-codes-and-standards/list-of-codes-and-standards?mode=code&code=2
​
[25] Howell, K., Dinan, S. Solyndra Misled government to get $535M solar project loan: report. The Washington Post. http://www.washingtontimes.com/news/2015/aug/26/solyndra-misled-government-get-535-million-solar-p/ (2015).
​
​
​
​
​